Listen up, folks! If you've ever wondered what makes machines move with precision and power, then you're in the right place. Response motors are the unsung heroes behind countless innovations we rely on daily. From industrial machinery to household appliances, these motors play a crucial role in transforming electrical energy into mechanical motion. And trust me, there's a lot more to them than meets the eye.
Think about it—when you press a button or flip a switch, something magical happens. That's where response motors step in, delivering the exact movement needed to get the job done. Whether it's spinning a fan blade or powering a conveyor belt, these motors are designed to respond quickly and efficiently. But hey, don't just take my word for it—there's a whole world of science and engineering behind their performance.
Now, buckle up because we're diving deep into the fascinating realm of response motors. By the end of this guide, you'll not only understand how they work but also why they're so important in modern technology. So, whether you're a tech enthusiast, an engineer, or just someone curious about the mechanics of motion, this article has got you covered.
- Applebees In Totowa Your Goto Spot For Comfort Food And Great Vibes
- Merry Christmas African American Images Celebrate The Spirit Of Diversity
What Are Response Motors?
Alright, let's break it down. Response motors, also known as servo motors or precision motors, are specialized devices that convert electrical energy into precise mechanical motion. Unlike regular motors, these bad boys are built for accuracy and control. They're like the ninjas of the motor world—silent, swift, and deadly accurate.
Here's the deal: response motors are equipped with feedback systems that allow them to adjust their performance in real-time. This means they can maintain exact speed, position, and torque, making them ideal for applications where precision matters. Think robotics, CNC machines, and even those fancy drones you see zipping around.
But what makes them tick? Well, it all comes down to their design. These motors are typically smaller, lighter, and more efficient than traditional motors. They're powered by advanced algorithms and sensors that ensure they operate at peak performance. In short, they're the cream of the crop when it comes to motor technology.
- Is Billie Eilish Dating Anyone Right Now Unveiling The Truth Behind Her Love Life
- Kate Middletons Guide To Wearing An Eternity Ring Style Tips And More
Key Features of Response Motors
- Precision Control: These motors can adjust their position and speed with remarkable accuracy.
- High Efficiency: They're designed to use energy wisely, minimizing waste and maximizing output.
- Compact Design: Despite their power, response motors are often small and lightweight, making them perfect for tight spaces.
- Reliability: Built to last, these motors can handle demanding tasks without breaking a sweat.
How Do Response Motors Work?
Now that we know what response motors are, let's talk about how they actually work. It's like a well-orchestrated dance between electrical signals and mechanical movement. At the heart of every response motor is a control system that manages its operation. This system uses feedback loops to monitor the motor's performance and make adjustments as needed.
Here's a quick rundown of the process:
- Command Input: The motor receives instructions from a controller, telling it what to do.
- Energy Conversion: Electrical energy is transformed into mechanical motion, driving the motor's components.
- Feedback Loop: Sensors monitor the motor's position and speed, sending data back to the controller.
- Adjustments: Based on the feedback, the controller fine-tunes the motor's performance to ensure precision.
It's a beautiful cycle of input, output, and correction. And the best part? It happens in the blink of an eye, allowing response motors to deliver smooth and accurate motion every time.
The Role of Feedback Systems
Feedback systems are the brains behind response motors. These systems use sensors to gather data about the motor's performance, such as its position, speed, and torque. This information is then sent to the controller, which uses it to make real-time adjustments.
Why is this important? Well, without feedback, a motor would have no way of knowing if it's meeting the desired specifications. It's like driving a car without a speedometer—you might think you're going the right speed, but you'd never really know for sure. Feedback systems ensure that response motors stay on track, delivering consistent and reliable performance.
Types of Response Motors
Not all response motors are created equal. Depending on the application, different types of motors are used to achieve specific results. Let's take a look at some of the most common types:
Brushless DC Motors
Brushless DC motors, or BLDC motors, are a popular choice for applications requiring high efficiency and low maintenance. They use electronic commutation instead of mechanical brushes, which reduces wear and tear. Plus, they're super quiet, making them ideal for noise-sensitive environments.
Stepper Motors
Stepper motors are another type of response motor that excels in precision. These motors move in discrete steps, allowing for exact control over position and speed. They're commonly used in 3D printers, CNC machines, and other applications where accuracy is key.
Servo Motors
Servo motors are the workhorses of the response motor family. They're designed for heavy-duty applications that require both power and precision. From industrial robots to aerospace systems, servo motors are the go-to choice for demanding tasks.
Applications of Response Motors
So, where do you find response motors in the real world? The answer is everywhere! These versatile devices are used in a wide range of industries and applications. Let's explore some of the most common uses:
Industrial Automation
In the world of manufacturing, response motors are the backbone of automation. They power conveyor belts, robotic arms, and assembly lines, ensuring that production runs smoothly and efficiently. Without them, modern factories would grind to a halt.
Consumer Electronics
From smartphones to washing machines, response motors are hidden in many of the gadgets we use every day. They help cameras focus, fans spin, and printers print—all with pinpoint accuracy.
Aerospace and Defense
When it comes to high-stakes applications like aerospace and defense, precision is non-negotiable. Response motors are used in everything from satellite systems to missile guidance, ensuring that critical operations are carried out with exactness.
Benefits of Using Response Motors
Why choose response motors over other types of motors? The answer lies in their unique advantages. Here are some of the key benefits:
- Precision: Response motors deliver exact control over position, speed, and torque.
- Efficiency: They're designed to use energy efficiently, reducing costs and environmental impact.
- Reliability: Built to last, these motors can handle demanding tasks without breaking down.
- Versatility: Response motors can be customized for a wide range of applications, from small devices to large machinery.
Comparing Response Motors to Traditional Motors
While traditional motors have their place, response motors offer several advantages. For one, they're more precise and efficient, making them better suited for modern applications. Plus, their compact design allows them to fit into spaces where larger motors simply won't go.
That's not to say traditional motors are obsolete—far from it. But for applications where accuracy and control are paramount, response motors are the clear winner.
Challenges and Considerations
Of course, no technology is perfect. Response motors come with their own set of challenges and considerations. Here are a few things to keep in mind:
Cost
Response motors can be more expensive than traditional motors, especially for high-performance models. However, their long-term benefits often outweigh the initial cost.
Complexity
Because they rely on advanced control systems, response motors can be more complex to set up and maintain. This requires specialized knowledge and expertise, which may not be available in all situations.
Maintenance
While response motors are built to last, they still require regular maintenance to ensure optimal performance. This includes checking sensors, replacing worn parts, and updating software as needed.
Future Trends in Response Motors
As technology continues to evolve, so do response motors. Here are some exciting trends to watch for:
AI Integration
Artificial intelligence is revolutionizing the way response motors operate. By incorporating AI into control systems, motors can learn and adapt to changing conditions, improving their performance over time.
Energy Efficiency
With growing concerns about climate change, manufacturers are focusing on making response motors even more energy-efficient. This includes using advanced materials and designs to reduce power consumption.
Miniaturization
As devices get smaller, so do the motors that power them. Engineers are working on creating response motors that are tinier and more powerful than ever before, opening up new possibilities for innovation.
Conclusion
And there you have it—a comprehensive guide to response motors. From their inner workings to their real-world applications, these incredible devices are shaping the future of technology. Whether you're an engineer, a tech enthusiast, or just someone curious about how things work, response motors are definitely worth exploring.
So, what's next? If you've found this article helpful, why not share it with your friends and colleagues? And if you have any questions or comments, feel free to drop them below. Let's keep the conversation going and continue learning together!
Table of Contents
- Down Curly Hair For Wedding Your Ultimate Guide To Stunning Bridal Hairstyles
- Esther Kim The Rising Star In The World Of Entertainment
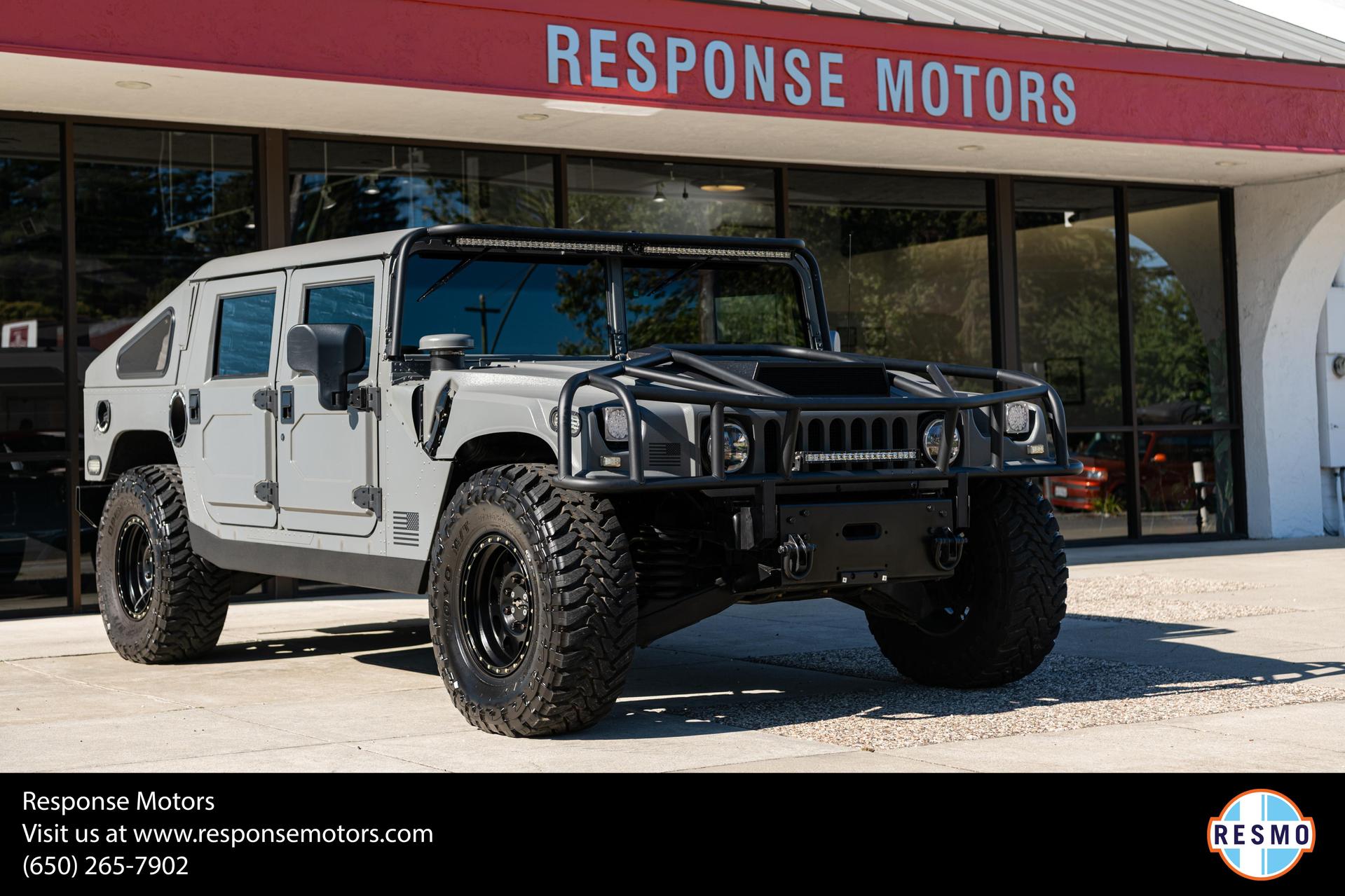
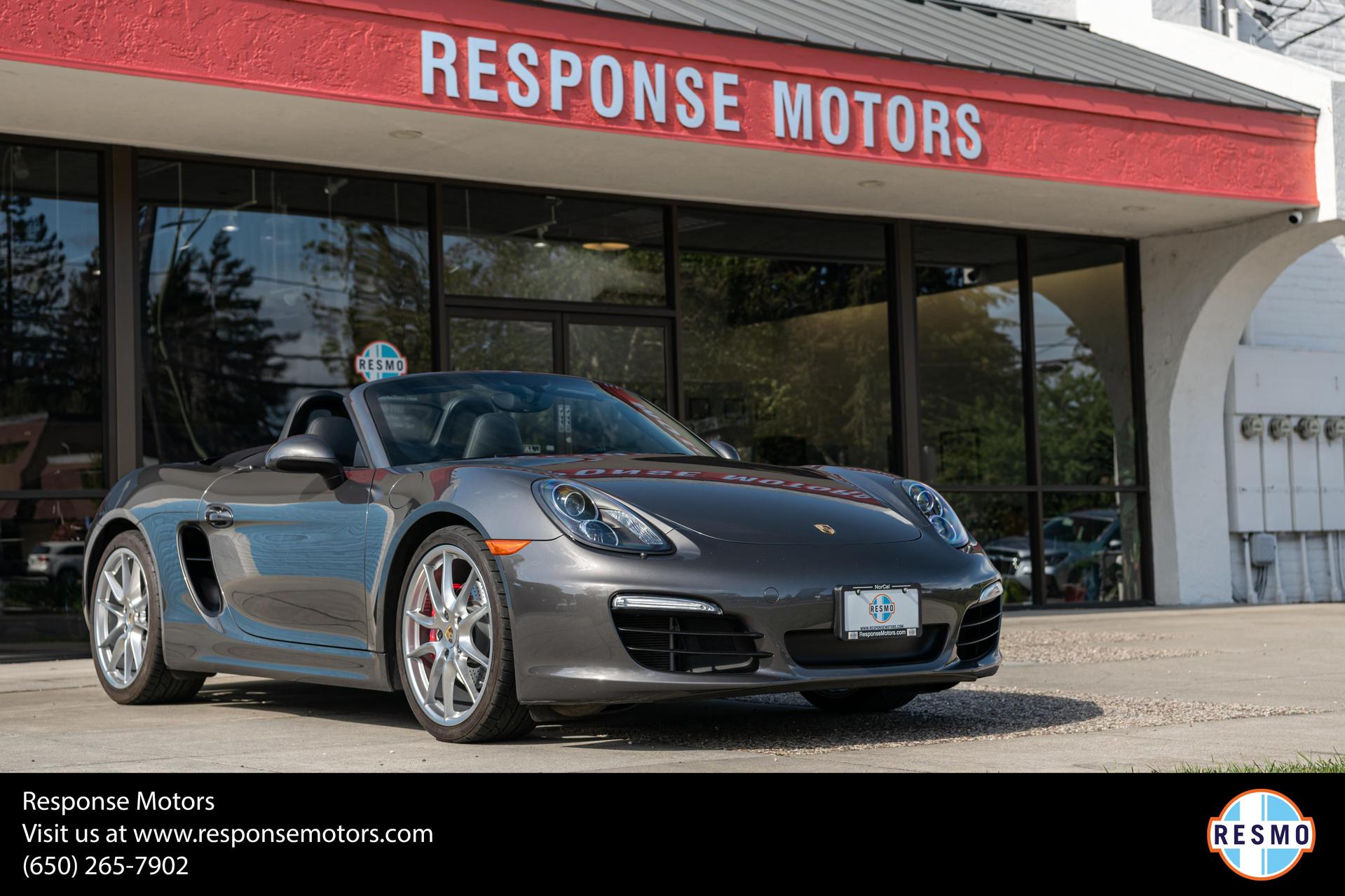